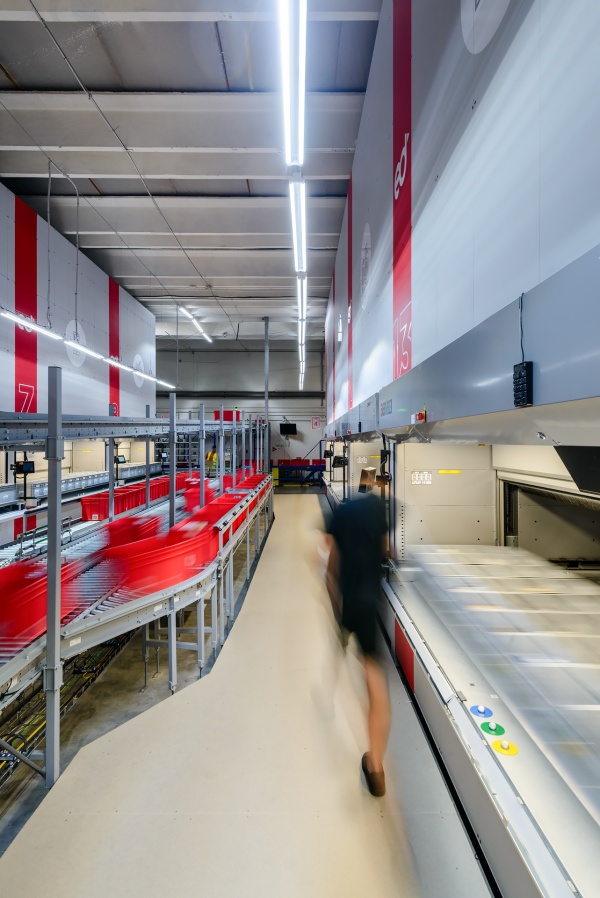
The company eD System is a leader in providing a distribution ecosystem in Central Europe. It offers 135,000 products from 300 brands, which are stored on 20,000 m2 of its own warehouse space. Every day, over 10,000 shipments are dispatched to the Czech, Polish and Slovak markets. In August 2021, eD System decided to build a new automated warehouse for storage and picking. Project preparation began in June 2022 in cooperation with sister companies LogTech and VertiFlex, which have combined their know-how in automation, vertical storage systems and conveyor solutions.
The primary objective of the project was to automate and streamline picking processes and increase order handling capacity, corresponding to the company's continuous growth. The brief to the prospective supplier was to supply a vertical storage system for the storage of electronics with a minimum volume of 600 m3 on trays with a minimum load capacity of 300 kg. The goods will be stored in plastic boxes of various sizes with barcodes. The system supplied shall be controlled by proprietary software with a link to the company's WMS. The control system must be able to control not only the vertical storage lifts but also the Pick-to-Light technology and the roller conveyor operator. Each vertical storage lift shall be equipped with its own automatic fire suppression system and be linked to a remote management system for remote diagnostics and servicing. The available ceiling height was just over six metres. Maximum emphasis was placed on the shortest possible picking time for ordered goods.
Design of the picking system
The design of the optimal solution involved the installation of 16 vertical storage lifts integrated into a conveyor system with a roller conveyor, four picking zones and 12 pick-to-light positions. The vertical storage lifts are divided into work zones of four and each machine is equipped with pick position indication, pick quantity, pick confirmation and control software display. The goods are picked according to the instructions of the control software and the Pick-to-Light technology into 600 x 400 x 320 mm bar-coded plastic transport bins.
Each picking station contains 12 positions dedicated to the placement of transport bins. Each position is equipped with a Pick-to-Light bar and allows identification of the bin. Once the picking process is complete, the transport bin is automatically sent to the circulating conveyor oval and then to the picking line at other workstations or to the shipping carton repacking station. The empty bins are then automatically transported back to the entry workstation where they are reloaded and released into the picking process. The shipping carton with the goods is automatically transported from the repacking station to the existing transport lines. The system guarantees a throughput of at least 1,000 lines processed per hour and runs in a two-shift operation 5 days a week.
VertiNode Ai - the heart of the system
VertiNode Ai is a dedicated control software for automated logistics with the latest artificial intelligence technology and compatible with most warehouse systems, developed by VertiFlex's in-house software team. In this project, the VertiNode Ai control software communicates with the parent WMS and provides two-way information exchange between the vertical storage lifts control system, dispatch conveyor line, Pick-to-Light technology and other interconnected technologies with the ERP.
Compact vertical storage lifts
The core of the system consists of 16 Compact vertical storage lifts from Swedish manufacturer Weland Solutions. Half of the machines are the 6,176 mm high Compact Twin lift model. The tray has a depth of 820 mm and a width of 3,660 mm. Each machine contains up to 44 trays. The vertical storage lifts have a bespoke, individualised design in the colors of eD System.
Two lifts are more than one
Twin technology completely changes the game in vertical storage. Compact Twin machines feature a lift with two positions above each other, allowing up to 30% more picking compared to a single-storey lift. Whilst one tray is exposed for picking, the lift prepares another tray in the second position in between, and when the first tray is finished, the operator simply swaps the two trays, the operator continues the picking process and the vertical storage lifts meanwhile puts the first tray in place and prepares the next tray for the holding position. As a result, the picking process becomes significantly faster and more efficient when handling orders. Thanks to Twin technology, the machines achieve up to twice the picking speed.
Another indisputable advantage of the twin lift is the maximum use of the vertical storage lift's storage space. The second lift position is located below the drive and thus reaches almost to the ground. This means that it is possible to place trays where a conventional single position extractor cannot reach. Depending on the material's height, this can create up to 5% additional storage space in each unit compared to traditional solutions. And when you multiply that by 8? Or even 16? That's another significant amount of storage space.
Two trays in a row
The other eight machines are the Compact Double model, which, in addition to the double lift, also has double depth with two trays of storage behind it. Included in the delivery for this project were Compact Double machines measuring 3,660 x 820 x 6,176 mm. With a machine height of over six metres and a total depth of 4,898 mm, there is space for up to 88 trays, depending on the height of the stored goods.
The double storage depth creates even more storage space in a limited floor area. By increasing the floor space occupied by the machine by 65%, we can create 100% more storage space. The Compact Double vertical storage lift is equipped with Twin technology, which allows the trays to be moved between different positions in order to remove trays from more distant positions. With high-volume items placed on trays closer to the lift, picking speeds are fully comparable to the Compact Twin vertical storage lift. With twice the number of trays, the Compact Double takes up less floor space than two Compact Twin vertical storage lifts, resulting in a more efficient use of storage space and optimised costs per square metre of storage.
Goods are stored on the trays in plastic bins that are marked with a barcode and alphanumeric code. Four bins sizes are used: 200 x 150 x 120 mm, 300 x 200 x 170 mm, 400 x 300 x 270 mm and 600 x 400 x 320 mm. The total number of bins has reached 20 000. All vertical storage lifts are equipped with a fire sensor connected to the EPS and an integrated automatic fire protection device.
The vertical storage lifts also have a range of visual and confirmation features to ensure minimal picking errors. Monitors are located at the top of the picking opening to provide information about the goods, their position on the tray and a photo of the specific item. Below the tray extension are coloured confirmation buttons indicating the picking status. The visual elements are complemented at the picking positions by coloured Pick-to-Light bars for completing the picking operation by placing the goods in the box and confirming it.
A complete novelty is the full-colour RGB bar, which is fitted to all machines. The bar is equipped with a programmable screen that displays important information such as the number of picked items and picking history. The entire bar is fully programmable and completely customizable to the unique requirements and needs of the individual customer.
Central roller conveyor with picking stations
The backbone of the new automated storage and picking zone is the conveyor line to which the individual workstations are connected. The entry point is the receiving workstation, which is used to match the shipping labels with the barcode of the bin, to log workers into the individual workstations and to start the processes at the individual workstations.
Four picking workstations with Vertinode Ai control terminals and 12 picking positions with Pick-to-Light confirmation buttons are connected to the conveyor line. Each station has a capacity of 200 picking operations per hour per worker. Based on the packing slips assigned to each bin, the VertiNode Ai software calls up bins in the ideal order to prioritize the bins that will free up picking zone capacity faster.
A fifth picking zone is reserved for items that are picked from locations other than the 4 vertical storage lifts zones. The workstation is also used to handle bins with error messages. Other workstations include a transfer rack, automatic entry scale, and an inspection workstation equipped with cameras. The repacking workstation is used to transfer goods from the shipping zones into plastic bins and to divide the bins into loading carts based on each zone.
A service roller track with a circulation oval ensures the connection of the individual workstations for the smooth transport of the bins until they are completely picked. Additionally, it includes a return branch dedicated to transporting empty shipping bins back to the receiving workstation.
Service, support and warranty
We provide a complete preventive service program ensuring smooth operation and minimizing the risk of downtime. All vertical storage lifts are connected to a remote access and management system for remote diagnostics and service. The response time for direct priority service interventions is within 4 hours of reporting a fault in 16/5 mode. A dedicated service hotline is also available to the customer in this mode. The entire system is guaranteed for 24 months.
A few numbers to finish
The entire project, from project preparation through the finalization of project documentation, and approval process to the installation and commissioning of the system took more than 14 months. Finally, the entire solution went through a rigorous testing and load testing process to ensure that all operations ran smoothly even under maximum traffic load during seasonal peaks. After the pilot phase, the entire system is connected to the proper operation of the entire warehouse.
The delivered solution covers an impressive 2,712 m², providing a storage capacity of more than 18,000 SKUs. The vertical storage lifts are equipped with a total of 907 trays. The average transport time of a new tray to the site is 21 seconds for the Compact Twin storage lifts. The picking capacity per operator is 200 operations per hour. The entire system offers a picking capacity of up to 3,000 operations per hour.
Integrating all parts of the system into one functional unit was undoubtedly a challenge. Many years of experience in the field of automation and integration on the part of the supplier companies LogTech and VertiFlex and the project manager Martin Řehor contributed significantly to its implementation. On the other hand, it was the enlightened approach to the automation of operations on the part of eD System and the maximum cooperation of all parties involved. You can read Bohuslav Kaněra, eD System's Director of Logistics, comment on the automated logistics solution here.